Concrete coatings transform dull, boring, and old concrete surfaces into durable, attractive, and long-lasting floors.
However, the process of applying concrete coatings can be complex, and mistakes lead to unsatisfactory results and thousands of dollars in costly repairs.
As a concrete coating company since 2018 in Waukesha, we’re often called to cleanup the mess that other companies and people make for homeowners.
So before you have to call us to fix it, here are some of the most common mistakes made during concrete coating applications and how to avoid them:
Bad Surface Preparation
One of the biggest mistakes in concrete coating applications is poor surface preparation.
Preparing the concrete surface is crucial for ensuring the coating adheres correctly.
This preparation involves cleaning the surface thoroughly, repairing cracks and damages, and ensuring the surface is level.
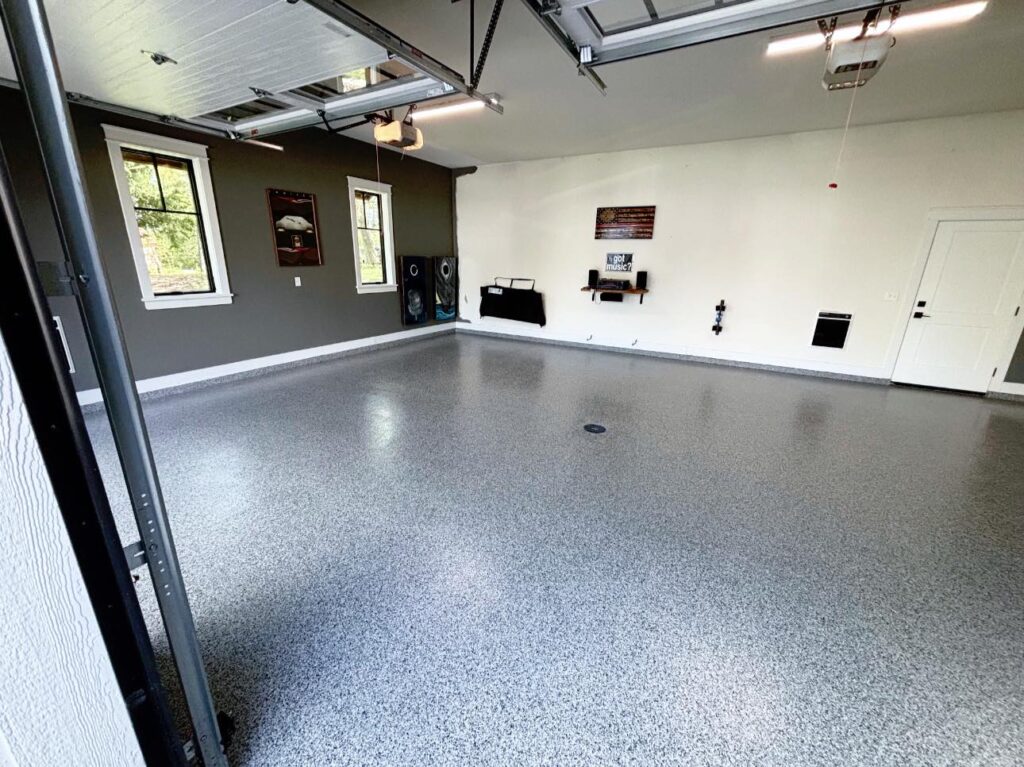
Skipping any of these steps can lead to poor adhesion, which might cause the coating to peel or bubble like you see in many old concrete floors which haven’t been treated.
The importance of surface preparation cannot be overstated.
For instance, a floor with residual oils or grease from an older kitchen must be cleaned meticulously, often using degreasers and industrial-grade cleaners, before any coating is applied.
If these contaminants aren’t removed, they can prevent the coating from bonding correctly with the concrete, leading to detachment and flaking.
And if the concrete has previously been sealed, the old sealant must be completely stripped to ensure the new coating adheres properly.
Ignoring Moisture Issues
Thankfully in southern Wisconsin, this isn’t as big of an issue as in places like Florida.
Even so, concrete can retain moisture, which is detrimental to the coating process.
Applying a coating over a damp concrete surface can trap moisture, leading to issues like blistering or delamination.
Moisture in concrete can come from high humidity or direct contact with water, and it can be particularly deceptive because it may not be visible on the surface.
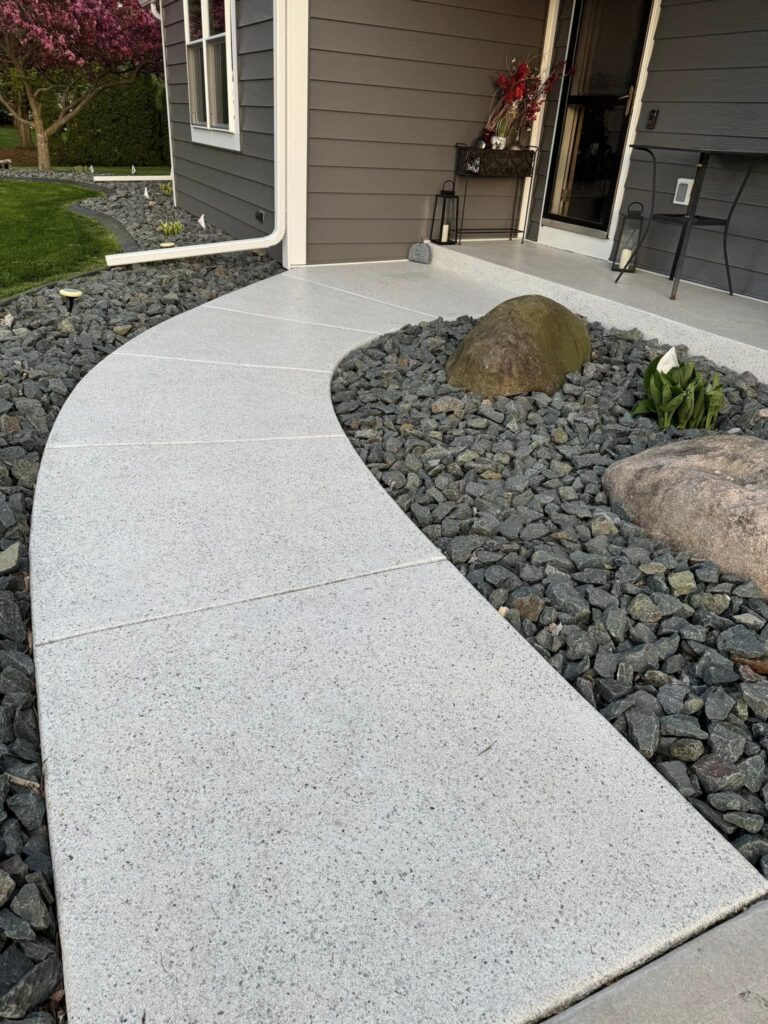
One effective method for testing moisture is the calcium chloride test, which measures the amount of moisture vapor emitting from the concrete.
A sports facility outside Waukesha once faced peeling issues when the coating was applied without this moisture test, leading to moisture vapor pushing upwards and causing the coating to bubble.
It’s essential to test the concrete for moisture and ensure it’s completely dry before proceeding with the application, which is one of the many reasons you should hire a professional for this.
Applying Coatings in Unsuitable Weather Conditions
Let’s be honest – you probably won’t find us applying coatings during a Wisconsin snowstorm.
But that aside, the weather plays a significant role in the success of a concrete coating application.
High humidity can prevent the coating from curing correctly, while cold weather can slow down the curing process.
It’s best to apply concrete coatings in dry, mild conditions and to follow standard recommendations regarding temperature and humidity.
A residential garage project in a cold climate saw the epoxy coating remain tacky for weeks because it was applied at temperatures below the recommended range.
Using temperature-controlled environments or choosing the right season for application can mitigate these issues and is preferred.
Incorrect Mixing and Application
Concrete coatings often come in multiple parts that need to be mixed together before application.
Incorrect mixing can lead to an uneven finish, poor coloration, or failure of the coating to set properly.
Application techniques also play a significant role.
For instance, using a roller that is too aggressive can introduce air bubbles into the coating, leading to a finish with tons of pinholes.
In contrast, a too-gentle technique might not adequately spread the coating, resulting in thin areas that wear out prematurely.
It’s important for the coating company to make sure they’re using the correct flake colors for the project too – making sure that the floor looks and feels as the customer wants.
We’ve seen far too many concrete coating companies disregard what customers want and use their flake colors instead of giving the customers a choice.
And while it might not impact the safety or result of the concrete itself, the person who’s ordering the coatings should get a say, no?
Applying Coatings Too Thickly or Thinly
The thickness of the coating should be consistent across the board.
Applying the coating too thickly can lead to issues like bubbling and cracking, while too thin an application might not offer enough protection or might wear out quickly.
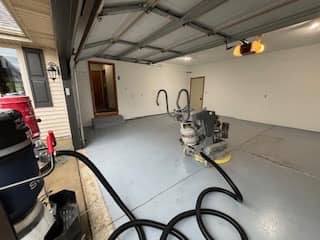
Using the right tools, such as squeegees or rollers, can help ensure a consistent thickness.
This also depends greatly on the place that’s being coated.
For example, we’d apply a thicker coat to an outdoor area like a patio instead of a kitchen, since being outdoors means it should have greater protection from the elements.
Applying a coating too thickly can lead to solvent entrapment, where solvents in the coating cannot evaporate properly, causing the surface to crack or bubble.
An automotive workshop faced this issue when the epoxy was applied too thickly, resulting in unsightly bubbles that compromised the floor’s smoothness and durability.
On the other hand, applying the coating too thinly can fail to protect the concrete adequately.
For example, a thin application in a high-traffic retail store led to rapid wear and tear, requiring a re-coating much sooner than anticipated. Using gauges to measure coating thickness during application can help achieve the correct specification and ensure long-term durability.
Lack of Proper Safety Measures
Concrete coating applications involve chemicals that can be hazardous if not handled correctly.
We use these chemicals everyday and failing to use appropriate safety gear such as gloves, masks, and eye protection can lead to accidents. This is why us (or any other concrete coating company) cares so much about safety.
Ensuring the workspace is well-ventilated is crucial to prevent inhalation of fumes, which is why many coating companies refuse to work on small environments.
Without proper ventilation, volatile organic compounds (VOCs) can accumulate, posing health risks to workers and others in the vicinity.
A project in an enclosed warehouse without adequate ventilation saw workers experience headaches and dizziness, highlighting the need for effective air management systems during application.
Personal protective equipment (PPE) is also vital.
Skin or eye contact with harsh chemicals can lead to severe irritation or burns.
Ensuring that all personnel are equipped with appropriate safety gear, such as respirators, gloves, and goggles, can prevent such accidents and promote a safer working environment.
These mistakes cost you thousands of dollars in damages.
One of the most googled concrete coating questions is “Can I do concrete coatings?”.
To be clear: concrete coatings are not DIY projects.
For your own safety and to avoid thousands of dollars in damages, it’s recommended you hire professionals like us or others in your local area to get the job done right.
If you have any questions, please feel free to call us at (262)-683-5381